Aromatics Production: Simplified
- patentpendingtexas
- Apr 7, 2019
- 3 min read
BTX refers to the aromatic compounds produced at an oil refinery - benzene, toluene, and xylene. The feedstock for a classic aromatics complex is primarily naphtha. Naphtha is a component fraction (5-10 volume % per barrel) of crude oil that is separated via distillation at a cut point of 220-315 °F. Naphtha is a low-octane mixture of paraffins (saturated hydrocarbons/alkanes), naphthenes (alicyclic hydrocarbons), and aromatics, in the C6 to C9 range.
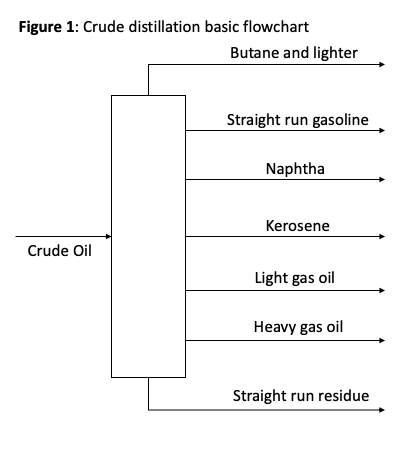
In an aromatics complex, a Naphtha Hydrotreater removes sulfur, nitrogen, and metal contaminants from the feed before passing on treated naphtha to a Catalytic Reforming unit. Hydrotreating naphtha protects the cat reformer reactor catalyst, improves conversion rates, and adheres to environmental regulations. The purpose of the catalytic (cat) reformer is demonstrated in the material balance below, resulting in an overall increase in octane number (gasoline blends with higher octane numbers result in minimal ‘knocking’ in engine cylinders, leading to improved efficiency in terms of mileage and motive power). Paraffins are converted to iso-paraffins, iso-paraffins are converted to naphthenes, and naphthenes are converted to aromatics. The cat reformer unit includes catalyst packed reactors through which naphtha is pumped at 800-950 °F and 200-800 psi, according to design. The exit stream from the reformer is called reformate. The reformate contains “reformed” naphtha high in octane, making it suitable to blend with gasoline. Since the reformate is also high in aromatics, it is pumped downstream to separate the BTX compounds.

Aromatics production is based on two simple principles; distillation & liquid-liquid extraction. First, the boiling points of benzene, toluene, and xylenes must be identified.
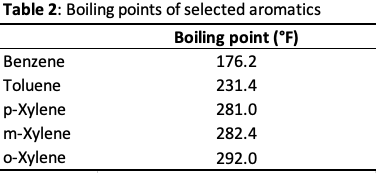
Since benzene has the lowest boiling point in the aromatics mix, it must be separated first followed by toluene, and xylene. Straight distillation will require numerous columns and high energy costs because there are a number of compounds in the reformate that boil at temperatures close to that of benzene. Therefore, liquid-liquid extraction is employed. Solvents such as sulfolane, diethylene glycol, or n-methyl pyrrolidone can be used to extract/dissolve the benzene, leaving behind the rest of the components in the benzene-stripped feed, or “raffinate”. The benzene-rich solvent can now be separated by distillation because the solvent has a much higher boiling point than the benzene. The raffinate can be used as a gasoline blend and the solvent can be recycled back to the extraction process. Toluene and xylene follow the same separation technique.

The above diagram oversimplifies the process steps, including the solvent extraction and subsequent aromatics recovery. The following diagram illustrates aromatics separation in more detail.

The 'benzene concentrating columns' take reformate as feed and produce three streams: 1) heavy reformate with a boiling point greater than that of benzene i.e. the stream includes toluene and xylenes, which is fed to toluene and xylene extraction trains. 2) light reformate with a boiling point less than that of benzene i.e. practically 'raffinate' because the stream does not contain aromatics. 3) benzene concentrate i.e. this stream contains compounds around the boiling point of benzene. The benzene concentrate is fed to a rotating disk contactor column which contains the extractive solvent. The extractor column produces two streams - raffinate & benzene-laden solvent. The solvent recovery column provides a substantially pure benzene stream.
The heavy reformate from the benzene concentrating columns is fed to an identical toluene extraction system where streams are dictated by the desired boiling range of toluene. A toluene stream is produced as well as a heavier reformate stream that is directed to a similar xylene extraction system, with the only difference being that xylene isomers boil over a range of temperatures. Therefore, the resultant product is a concentrated mixture of xylene isomers, which undergo further separation.
References:
1) Handbook of Petroleum Refining Processes by Robert A. Meyers
2) Petroleum Refining: Technology & Economics by Glenn E. Handwerk
3) Petroleum Processing Handbook by John J. McKetta
4) U.S. Patent 3,434,087 - Recovery of Aromatics
5) U.S. Patent 3,173,966 - Solvent Extraction Process for Recovery of Aromatic Hydrocarbons
6) U.S. Patent 3,114,783 - Separation of Aromatics from Hydrocarbon Streams
7) U.S. Patent 3,862,254 - Production of Aromatic Hydrocarbons
8) U.S. Patent 4,353,794 - Process for the Solvent Extraction of Aromatics and the Recovery of an Aromatics-free Non-aromatic Product From a Hydrocarbon Feedstock
Comments